In a typical waste paper recycling line for manufacturing writing – printing paper, newsprint tissue corrugated medium, liner board and carton board, even after having fine screening of the stock, some specks, laques, hot melts etc still exists in stock. To get rid of these impurities, the ultimate solution is hot dispersion system. The system comprises of following three major equipments :
1) Twin wire press
2) Conveying and heating screws
3) Disc Disperser
The stock after having screened and deinked is fed to the twin press @ 4% cy. for the purpose of dewatering and there by getting higher cy. i.e. 30% .The significant feature of this equipment are less power consumption and a very good filtrate water quality. This dewatered stock of 30% cy. is passed through various screws including heating screw in order to get the stock temperature as high as 120C. Such high temperature (upto 120C)” re-cooks” fibers, which develop more flexibility and makes them more resistant.
Also the starch coming from coated waste paper is cooked again, thus regenerates its characteristics. After passing through heating screw, the stock is fed to Disc Disperser through feeding screw. At high temperature high shear force on sharp teeth dispersing discs and very low disc gap means of high precision electohydraulic arrangement with an accuracy of 0.01mm, the impurities such as specks, laques, hot melts etc. get dispersed and makes stock suitable for the bleaching stage. It reduces drastically the size of sticky particles in order to prevent any problem in the machine. Further, these heated fibers pass through a very small gap without getting any cutting action such as refiner. Thus, the inherent strength properties of the fibers remain unaffected.
A) Sample of Papersheet at the Inlet of Hot dispenser system
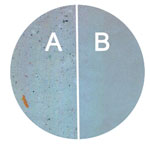
Distinct Advantages of Hot Dispersion System :
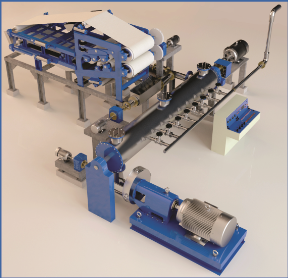